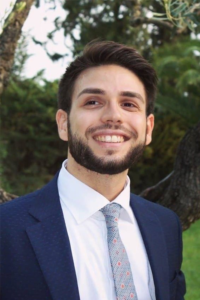
Information
+39 080 596 3843
ti.ab1745590351ilop@1745590351azzob1745590351.otsu1745590351gua1745590351
Scopus Researcher Page
Curriculum Vitae (english)
Publications
Augusto BOZZA
PhD student
Augusto Bozza received the Bachelor Degree in Computer Science and Automation Engineering in October 2018 and the Master Degree with honours in Automation Engineering (with specialization in Robotics) in April 2021, both from the Polytechnic of Bari. He has been a graduate Research Assistant from June to October 2021 at the Decision and Control Laboratory of Department of Electrical and Information Engineering of Polytechnic of Bari.
He is currently working toward the Ph.D. degree in Electrical and Information Engineering of the same university under the supervision of Prof. Engr. Mariagrazia Dotoli. His research interests include modelling, control, and simulation of manufacturing and industrial systems based on the Digital Twin (DT) framework.
Publications
2024
- Bozza, A., Martin, T., Cavone, G., Carli, R., Dotoli, M. & Allgower, F. (2024) Online Data-Driven Control of Nonlinear Systems Using Semidefinite Programming. IN IEEE Control Systems Letters, 8.3189 – 3194. doi:10.1109/LCSYS.2024.3521645
[BibTeX] [Abstract] [Download PDF]This letter proposes a novel Data-Driven (DD) method for controlling unknown input-affine nonlinear systems. First, we estimate the system dynamics from noisy data offline through Subspace Identification of Nonlinear Dynamics. Then, at each time step during runtime, we exploit this estimation to deduce a feedback-linearization control law that robustly regulates all the systems consistent with the data. Notably, the control law is derived by solving a Semidefinite Programming (SDP) online. Moreover, closed-loop stability is ensured by constraining a Lyapunov function to descend in each time step using a linear-matrix-inequality representation. Unlike related DD control approaches for nonlinear systems based on SDP, our approach does not require any approximation of the nonlinear dynamics, while requiring the knowledge of a library of candidate basis functions. Finally, we validate our theoretical contributions by simulations for stabilization and tracking, outperforming another DD literature-inspired controller. © 2017 IEEE.
@ARTICLE{Bozza20243189, author = {Bozza, Augusto and Martin, Tim and Cavone, Graziana and Carli, Raffaele and Dotoli, Mariagrazia and Allgower, Frank}, title = {Online Data-Driven Control of Nonlinear Systems Using Semidefinite Programming}, year = {2024}, journal = {IEEE Control Systems Letters}, volume = {8}, pages = {3189 – 3194}, doi = {10.1109/LCSYS.2024.3521645}, url = {https://www.scopus.com/inward/record.uri?eid=2-s2.0-85213981931&doi=10.1109%2fLCSYS.2024.3521645&partnerID=40&md5=9a05eabfe1da3b7d0ea57ac940808f8d}, abstract = {This letter proposes a novel Data-Driven (DD) method for controlling unknown input-affine nonlinear systems. First, we estimate the system dynamics from noisy data offline through Subspace Identification of Nonlinear Dynamics. Then, at each time step during runtime, we exploit this estimation to deduce a feedback-linearization control law that robustly regulates all the systems consistent with the data. Notably, the control law is derived by solving a Semidefinite Programming (SDP) online. Moreover, closed-loop stability is ensured by constraining a Lyapunov function to descend in each time step using a linear-matrix-inequality representation. Unlike related DD control approaches for nonlinear systems based on SDP, our approach does not require any approximation of the nonlinear dynamics, while requiring the knowledge of a library of candidate basis functions. Finally, we validate our theoretical contributions by simulations for stabilization and tracking, outperforming another DD literature-inspired controller. © 2017 IEEE.}, author_keywords = {Data-driven control; feedback linearization; linear matrix inequality; semidefinite programming; subspace identification of nonlinear dynamics}, type = {Article}, publication_stage = {Final}, source = {Scopus}, note = {Cited by: 0; All Open Access, Hybrid Gold Open Access} }
2023
- Askari, B., Bozza, A., Cavone, G., Carli, R. & Dotoli, M. (2023) An adaptive constrained clustering approach for real-time fault detection of industrial systems. IN European Journal of Control, 74.. doi:10.1016/j.ejcon.2023.100858
[BibTeX] [Abstract] [Download PDF]Thanks to the pervasive deployment of sensors in Industry 4.0, data-driven methods are recently playing an important role in the fault diagnosis and prognosis of industrial systems. In this paper, a novel Adaptive Constrained Clustering algorithm is defined to support real-time fault detection of an industrial machine, by clustering the incoming monitoring data into two clusters over time, representing the nominal and non-nominal work conditions, respectively. To this aim, the proposed algorithm relies on a two-stage procedure: micro-clustering and constrained macro-clustering. The former stage is responsible for grouping the batches of work-cycle data into micro-clusters, while the data stream continuously arrives from the data acquisition system. Then, after condensing the micro-clusters into vectors of cluster features, and leveraging on additional knowledge on the nominal and non-nominal working conditions (i.e., constraints on some samples), the second stage aims at offline grouping the micro-clusters features into macro-clusters. Experimental results on a real-world industrial case study show that the proposed real time framework achieves the same results of offline baseline methods (e.g., Constrained K-means) with a higher responsiveness and processing speed; in comparison to stream baseline methods (e.g., Stream K-means), the proposed approach obtains more accurate and easily interpretable results. © 2023 European Control Association
@ARTICLE{Askari2023, author = {Askari, Bahman and Bozza, Augusto and Cavone, Graziana and Carli, Raffaele and Dotoli, Mariagrazia}, title = {An adaptive constrained clustering approach for real-time fault detection of industrial systems}, year = {2023}, journal = {European Journal of Control}, volume = {74}, doi = {10.1016/j.ejcon.2023.100858}, url = {https://www.scopus.com/inward/record.uri?eid=2-s2.0-85162877723&doi=10.1016%2fj.ejcon.2023.100858&partnerID=40&md5=e062207fcb506e79c37bedf7a930b430}, abstract = {Thanks to the pervasive deployment of sensors in Industry 4.0, data-driven methods are recently playing an important role in the fault diagnosis and prognosis of industrial systems. In this paper, a novel Adaptive Constrained Clustering algorithm is defined to support real-time fault detection of an industrial machine, by clustering the incoming monitoring data into two clusters over time, representing the nominal and non-nominal work conditions, respectively. To this aim, the proposed algorithm relies on a two-stage procedure: micro-clustering and constrained macro-clustering. The former stage is responsible for grouping the batches of work-cycle data into micro-clusters, while the data stream continuously arrives from the data acquisition system. Then, after condensing the micro-clusters into vectors of cluster features, and leveraging on additional knowledge on the nominal and non-nominal working conditions (i.e., constraints on some samples), the second stage aims at offline grouping the micro-clusters features into macro-clusters. Experimental results on a real-world industrial case study show that the proposed real time framework achieves the same results of offline baseline methods (e.g., Constrained K-means) with a higher responsiveness and processing speed; in comparison to stream baseline methods (e.g., Stream K-means), the proposed approach obtains more accurate and easily interpretable results. © 2023 European Control Association}, author_keywords = {Constrained clustering; Fault detection; Industrial systems; Machine learning; Stream clustering; Unsupervised learning}, type = {Article}, publication_stage = {Final}, source = {Scopus}, note = {Cited by: 4} }
- Bozza, A., Cavone, G., Carli, R. & Dotoli, M. (2023) A Power Electronic Converters-Inspired Approach for Modeling PWM Switched-Based Nonlinear Hydraulic Servo Actuators IN Conference Proceedings – IEEE International Conference on Systems, Man and Cybernetics., 2477 – 2482. doi:10.1109/SMC53992.2023.10394065
[BibTeX] [Abstract] [Download PDF]This paper investigates a novel approach for properly modeling Hydraulic Servo Actuators (HSAs) based on ON-OFF switching valves. HSAs represent very high efficiency and small size-to-power ratio hydraulic actuators. Their functioning is guaranteed by their control system that ensures the desired flow-rate, and consequently, the proper pressure, to be provided to the actuator’s chambers. Nevertheless, achieving a good model of such HSAs for control purposes is non-trivial, due to their hybrid nature inherited from the switching between the different operating modes produced by valves. To overcome this limit, we propose an average equivalent discrete-time model of the chambers’ pressure dynamics related to a single control input for the digital valves. The proposed model takes inspiration from the analogy existing between hydraulic systems and power electronic converters, and guarantees the same performance as the traditional model, with the advantage of greatly simplifying the control of the servo actuator. Finally, the consistency of the proposed model with respect to its nonlinear hybrid version is proved via numerical examples. © 2023 IEEE.
@CONFERENCE{Bozza20232477, author = {Bozza, Augusto and Cavone, Graziana and Carli, Raffaele and Dotoli, Mariagrazia}, title = {A Power Electronic Converters-Inspired Approach for Modeling PWM Switched-Based Nonlinear Hydraulic Servo Actuators}, year = {2023}, journal = {Conference Proceedings - IEEE International Conference on Systems, Man and Cybernetics}, pages = {2477 – 2482}, doi = {10.1109/SMC53992.2023.10394065}, url = {https://www.scopus.com/inward/record.uri?eid=2-s2.0-85187260571&doi=10.1109%2fSMC53992.2023.10394065&partnerID=40&md5=ba0c9a7b491927b01db552a62bd2d7de}, abstract = {This paper investigates a novel approach for properly modeling Hydraulic Servo Actuators (HSAs) based on ON-OFF switching valves. HSAs represent very high efficiency and small size-to-power ratio hydraulic actuators. Their functioning is guaranteed by their control system that ensures the desired flow-rate, and consequently, the proper pressure, to be provided to the actuator's chambers. Nevertheless, achieving a good model of such HSAs for control purposes is non-trivial, due to their hybrid nature inherited from the switching between the different operating modes produced by valves. To overcome this limit, we propose an average equivalent discrete-time model of the chambers' pressure dynamics related to a single control input for the digital valves. The proposed model takes inspiration from the analogy existing between hydraulic systems and power electronic converters, and guarantees the same performance as the traditional model, with the advantage of greatly simplifying the control of the servo actuator. Finally, the consistency of the proposed model with respect to its nonlinear hybrid version is proved via numerical examples. © 2023 IEEE.}, author_keywords = {Electro-Hydraulic Analogy; Hybrid Systems; Hydraulic Servo Actuators; Nonlinear Systems; Pulse Width Modulation (PWM); Switching Systems}, type = {Conference paper}, publication_stage = {Final}, source = {Scopus}, note = {Cited by: 1} }
2022
- Bozza, A., Askari, B., Cavone, G., Carli, R. & Dotoli, M. (2022) An Adaptive Model Predictive Control Approach for Position Tracking and Force Control of a Hydraulic Actuator IN IEEE International Conference on Automation Science and Engineering., 1029 – 1034. doi:10.1109/CASE49997.2022.9926645
[BibTeX] [Abstract] [Download PDF]This paper presents an Adaptive Model Predictive Control (AMPC) approach for the position tracking and force control of a hydraulic actuator (HA). Due to its nonlinear dynamics, the iterative linearization paradigm is employed to approximate the HA system by a linear time-varying model. Such a representation is used as the internal plant model of the predictive controller to effectively make predictions on the system state. The effectiveness of the proposed AMPC architecture is shown through numerical experiments addressing the control of a real HA on different scenarios. Finally, a comparative analysis on several values of sampling time, prediction and control horizon is carried out in order to investigate the effect of the parameters tuning on the performance of the closed-loop control system. © 2022 IEEE.
@CONFERENCE{Bozza20221029, author = {Bozza, Augusto and Askari, Bahman and Cavone, Graziana and Carli, Raffaele and Dotoli, Mariagrazia}, title = {An Adaptive Model Predictive Control Approach for Position Tracking and Force Control of a Hydraulic Actuator}, year = {2022}, journal = {IEEE International Conference on Automation Science and Engineering}, volume = {2022-August}, pages = {1029 – 1034}, doi = {10.1109/CASE49997.2022.9926645}, url = {https://www.scopus.com/inward/record.uri?eid=2-s2.0-85141675790&doi=10.1109%2fCASE49997.2022.9926645&partnerID=40&md5=8ea9bb1c05f9c04a733472aeef5755d1}, abstract = {This paper presents an Adaptive Model Predictive Control (AMPC) approach for the position tracking and force control of a hydraulic actuator (HA). Due to its nonlinear dynamics, the iterative linearization paradigm is employed to approximate the HA system by a linear time-varying model. Such a representation is used as the internal plant model of the predictive controller to effectively make predictions on the system state. The effectiveness of the proposed AMPC architecture is shown through numerical experiments addressing the control of a real HA on different scenarios. Finally, a comparative analysis on several values of sampling time, prediction and control horizon is carried out in order to investigate the effect of the parameters tuning on the performance of the closed-loop control system. © 2022 IEEE.}, author_keywords = {Adaptive MPC; Hydraulic Actuator; Model Linearization; Nonlinear Systems; Position and Force Tracking}, type = {Conference paper}, publication_stage = {Final}, source = {Scopus}, note = {Cited by: 4} }
- Cavone, G., Bozza, A., Carli, R. & Dotoli, M. (2022) MPC-Based Process Control of Deep Drawing: An Industry 4.0 Case Study in Automotive. IN IEEE Transactions on Automation Science and Engineering, 19.1586 – 1598. doi:10.1109/TASE.2022.3177362
[BibTeX] [Abstract] [Download PDF]Deep drawing is a metalworking procedure aimed at getting a cold metal sheet plastically deformed in accordance with a pre-defined mould. Although this procedure is well-established in industry, it is still susceptible to several issues affecting the quality of the stamped metal products. In order to reduce defects of workpieces, process control approaches can be performed. Typically, process control employs simple proportional-integral-derivative (PID) regulators that steer the blank holder force (BHF) based on the error on the punch force. However, a single PID can only control single-input single-output systems and cannot handle constraints on the process variables. Differently from the state of the art, in this paper we propose a process control architecture based on Model Predictive Control (MPC), which considers a multi-variable system model. In particular, we represent the deep drawing process with a single-input multiple-output Hammerstein-Wiener model that relates the BHF with the draw-in of $n$ different critical points around the die. This allows the avoidance of workpiece defects that are due to the abnormal sliding of the metal sheet during the forming phase. The effectiveness of the proposed process controller is shown on a real case study in a digital twin framework, where the performance achieved by the MPC-based system is analyzed in detail and compared against the results obtained through an ad-hoc defined multiple PID-based control architecture. Note to Practitioners – This work is motivated by the emerging need for the effective implementation of the zero-defect manufacturing paradigm in the Industry 4.0 framework. Especially in the deep drawing process, various quality issues in stamped parts can lead to significant product waste and manufacturing inefficiencies. This turns into considerable economic losses for companies, particularly in the automotive sector, where deep drawing is one of the most used cold sheet metal forming techniques. In most applications, only sample inspections are performed on batches of finished-product, with subsequent losses of time and resources. For the sake of improving the workpiece quality, innovative strategies for real-time process control represent a viable and promising solution. In this context, the proposed MPC-based process control approach allows the correct shaping of the metal sheet that is getting deformed during the forming stroke, thanks to the draw-in monitoring at various locations around the die. The draw-in is indeed one of the most effective forming variables to control in order to provide a correct BHF during the forming stroke. A useful and easy-to-implement non-linear metal sheet deep drawing process model is provided by this paper to perform an innovative process control strategy. A comprehensive methodology is applied in detail to an automotive case study, ranging from process modeling (model identification and validation based on experimental data acquisition) to MPC implementation (controller tuning and testing and software-in-the-loop system validation). The presented method can be easily implemented on any real deep drawing press, providing the multivariable constrained process with a suitable control system able to make the stamped parts well formed. © 2004-2012 IEEE.
@ARTICLE{Cavone20221586, author = {Cavone, Graziana and Bozza, Augusto and Carli, Raffaele and Dotoli, Mariagrazia}, title = {MPC-Based Process Control of Deep Drawing: An Industry 4.0 Case Study in Automotive}, year = {2022}, journal = {IEEE Transactions on Automation Science and Engineering}, volume = {19}, number = {3}, pages = {1586 – 1598}, doi = {10.1109/TASE.2022.3177362}, url = {https://www.scopus.com/inward/record.uri?eid=2-s2.0-85131727980&doi=10.1109%2fTASE.2022.3177362&partnerID=40&md5=689e5dd375cab07673634f266a278717}, abstract = {Deep drawing is a metalworking procedure aimed at getting a cold metal sheet plastically deformed in accordance with a pre-defined mould. Although this procedure is well-established in industry, it is still susceptible to several issues affecting the quality of the stamped metal products. In order to reduce defects of workpieces, process control approaches can be performed. Typically, process control employs simple proportional-integral-derivative (PID) regulators that steer the blank holder force (BHF) based on the error on the punch force. However, a single PID can only control single-input single-output systems and cannot handle constraints on the process variables. Differently from the state of the art, in this paper we propose a process control architecture based on Model Predictive Control (MPC), which considers a multi-variable system model. In particular, we represent the deep drawing process with a single-input multiple-output Hammerstein-Wiener model that relates the BHF with the draw-in of $n$ different critical points around the die. This allows the avoidance of workpiece defects that are due to the abnormal sliding of the metal sheet during the forming phase. The effectiveness of the proposed process controller is shown on a real case study in a digital twin framework, where the performance achieved by the MPC-based system is analyzed in detail and compared against the results obtained through an ad-hoc defined multiple PID-based control architecture. Note to Practitioners - This work is motivated by the emerging need for the effective implementation of the zero-defect manufacturing paradigm in the Industry 4.0 framework. Especially in the deep drawing process, various quality issues in stamped parts can lead to significant product waste and manufacturing inefficiencies. This turns into considerable economic losses for companies, particularly in the automotive sector, where deep drawing is one of the most used cold sheet metal forming techniques. In most applications, only sample inspections are performed on batches of finished-product, with subsequent losses of time and resources. For the sake of improving the workpiece quality, innovative strategies for real-time process control represent a viable and promising solution. In this context, the proposed MPC-based process control approach allows the correct shaping of the metal sheet that is getting deformed during the forming stroke, thanks to the draw-in monitoring at various locations around the die. The draw-in is indeed one of the most effective forming variables to control in order to provide a correct BHF during the forming stroke. A useful and easy-to-implement non-linear metal sheet deep drawing process model is provided by this paper to perform an innovative process control strategy. A comprehensive methodology is applied in detail to an automotive case study, ranging from process modeling (model identification and validation based on experimental data acquisition) to MPC implementation (controller tuning and testing and software-in-the-loop system validation). The presented method can be easily implemented on any real deep drawing press, providing the multivariable constrained process with a suitable control system able to make the stamped parts well formed. © 2004-2012 IEEE.}, author_keywords = {Metal deep drawing process control; model predictive control; real-time process control; software-in-the-loop simulation; zero-defect manufacturing}, type = {Article}, publication_stage = {Final}, source = {Scopus}, note = {Cited by: 26; All Open Access, Hybrid Gold Open Access} }
2021
- Bozza, A., Cavone, G., Carli, R., Mazzoccoli, L. & Dotoli, M. (2021) An MPC-based Approach for the Feedback Control of the Cold Sheet Metal Forming Process IN IEEE International Conference on Automation Science and Engineering., 286 – 291. doi:10.1109/CASE49439.2021.9551602
[BibTeX] [Abstract] [Download PDF]In the automotive sector the cold forming of metal sheets is one of the main production activities. However, it is also one of the main source of production wastes. The generally adopted strategy to reduce the number of abnormal stamped parts is the feedback control of the stamping press (i.e., the machine control), while the feedback control of the stamping process is rarely considered. The process control, differently from the press control, can allow the monitoring of the state of the stamped part during the formation phase and the provision of corrective actions in case of abnormal behaviors of the metal sheet, thus ensuring a more precise control of the process. In this context, this paper presents a novel methodology for the cold metal forming process control based on Model Predictive Control (MPC). Firstly, a dynamical model of the system is defined that describes the draw-in of n critical points of the metal sheet as a function of the Blank Holder Force (BHF) and the punch stroke. Then, two different MPC-based real-time controllers are built for two different types of press configuration: the monolithic and the differential one. In the first case, a mono-MPC control system evaluates the draw-in of n critical points and computes a single couple of control signals (i.e., the BHF and the punch stroke). In the second case, a multi-MPC control system computes n different couples of control signals, i.e., one for each monitored draw-in. Finally, a case study is presented with the aim to test both the architectures, considering several simulation scenarios (with or without external disturbances on the plant), in order to make a control system architectures comparison in terms of tracking errors and workpiece quality. © 2021 IEEE.
@CONFERENCE{Bozza2021286, author = {Bozza, Augusto and Cavone, Graziana and Carli, Raffaele and Mazzoccoli, Luigi and Dotoli, Mariagrazia}, title = {An MPC-based Approach for the Feedback Control of the Cold Sheet Metal Forming Process}, year = {2021}, journal = {IEEE International Conference on Automation Science and Engineering}, volume = {2021-August}, pages = {286 – 291}, doi = {10.1109/CASE49439.2021.9551602}, url = {https://www.scopus.com/inward/record.uri?eid=2-s2.0-85117041530&doi=10.1109%2fCASE49439.2021.9551602&partnerID=40&md5=8f6b0f6133565ad0c087ea675cf9c3b9}, abstract = {In the automotive sector the cold forming of metal sheets is one of the main production activities. However, it is also one of the main source of production wastes. The generally adopted strategy to reduce the number of abnormal stamped parts is the feedback control of the stamping press (i.e., the machine control), while the feedback control of the stamping process is rarely considered. The process control, differently from the press control, can allow the monitoring of the state of the stamped part during the formation phase and the provision of corrective actions in case of abnormal behaviors of the metal sheet, thus ensuring a more precise control of the process. In this context, this paper presents a novel methodology for the cold metal forming process control based on Model Predictive Control (MPC). Firstly, a dynamical model of the system is defined that describes the draw-in of n critical points of the metal sheet as a function of the Blank Holder Force (BHF) and the punch stroke. Then, two different MPC-based real-time controllers are built for two different types of press configuration: the monolithic and the differential one. In the first case, a mono-MPC control system evaluates the draw-in of n critical points and computes a single couple of control signals (i.e., the BHF and the punch stroke). In the second case, a multi-MPC control system computes n different couples of control signals, i.e., one for each monitored draw-in. Finally, a case study is presented with the aim to test both the architectures, considering several simulation scenarios (with or without external disturbances on the plant), in order to make a control system architectures comparison in terms of tracking errors and workpiece quality. © 2021 IEEE.}, author_keywords = {Metal forming; Model Predictive Control; process control; real-time feedback control}, type = {Conference paper}, publication_stage = {Final}, source = {Scopus}, note = {Cited by: 6} }